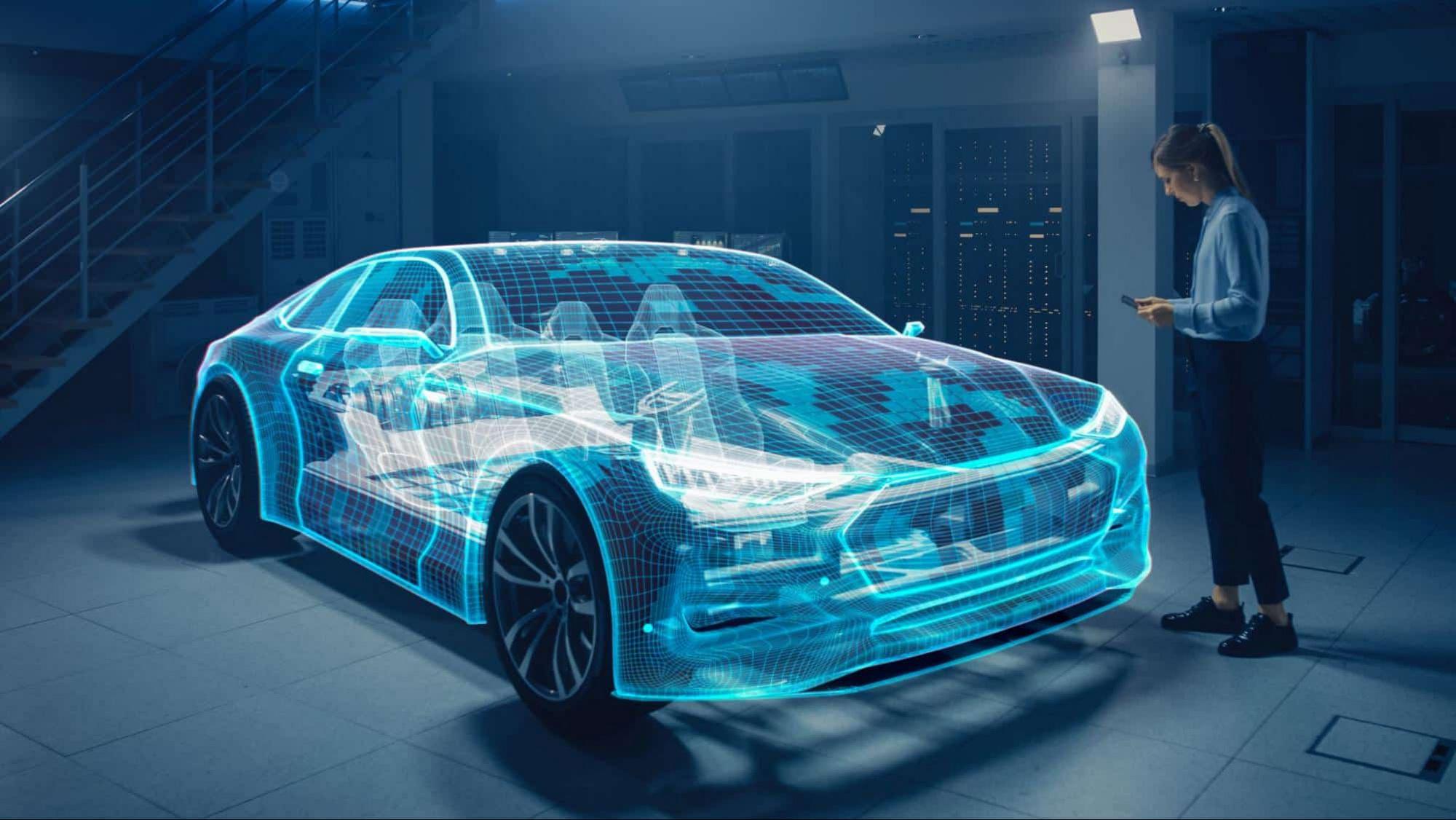
Designing and building better cars and planes with AI, data analytics and high performance computing in the cloud.
There are almost as many new cloud technologies driving the auto and aero industries as there are models of cars.
Google Cloud
This article originally appeared on Transform with Google Cloud.
When you look at a car—four wheels, a hood, red tail lights—or a plane—two wings, tiny windows, decorative tail fins—it’s amazing how much and how little has changed over a century of transportation innovation.
Now, both the automotive and aerospace industries are undergoing one of the greatest transformations since their inceptions. And what’s so striking about these epochal changes is how they are at once so digital and so physical. While cloud, AI, high-performance computing, and other advanced technologies have been busier and busier transforming every industry, whether finance or logistics, shopping or gaming, most of this innovation has been bringing things like our bank branches and leisure activities onto smaller screens and faster apps.
The changes afoot in automotive and aerospace are likewise about size and speed, but they are uniquely focused on continuing to advance how we move, better, faster, safer, and more sustainably, around the real world.
Volkswagen has invested $3 billion (so far) in its automotive software unit, CARIAD, since launching 18 months ago. GM is increasing its share in Cruise, and Ford has partnered with semiconductor manufacturer GlobalFoundries to work on R&D for chip design—the first time a car manufacturer has taken a direct investment in a chip company. It’s clear that technology plays an important role in the transformation of these companies. In aviation, Airbus has tech incubator Airbus BizLab, Lufthansa has its Innovation Hub, and Alaska announced a new incubator fund, to name a few examples.
When you combine advanced manufacturing techniques with the cloud, artificial intelligence, high performance computing, computer-aided design and engineering, and data analytics, you have all the building blocks for transformation. Factories are made more efficient. Supply chains can be optimized. Cars and planes are lighter and stronger and perform better.
Making this shift isn’t easy
For years now, organizations have used computer-aided design (CAD), computer-aided engineering (CAE), and generative design to optimize the design process. These tools can drastically reduce the need for physical prototypes and practical tests such as impact, fatigue, or failure in the automobile industry; increasing fuel efficiency of jet engines with thermodynamic modeling; simulating air bag deployment in cars to maximize safety; and blade off testing for certification of aircraft engines. The latest advances are using AI to go beyond, and instead CAE now often looks at whole systems and how different parts of it can be optimized to perform under certain conditions.
The main challenge when designing an automobile, aircraft engine, or electronic product with CAE is that it can take hours if not days to simulate conditions and outcomes with standard computer processing. And then even longer to run simulations of how all the parts work together in certain conditions, such as safety compliance scenarios or optimizing aerodynamics for energy efficiency.
Historically, CAE for designing complex products has been performed with expensive and power-hungry on-premises high-performance computing clusters. That’s been changing with a more efficient network that has decreased the latency between the cloud and the office. Auto manufacturers like Nissan and Toyota are now designing vehicles with high performance computing running in the cloud.
Continue reading this article at Transform with Google Cloud.